It’s Fall Break, but the Little Big Engineers toil on. Because the whole team will be gone for IAAPA in Week 11, and Lori will also be gone for two days of Week 10 for the Toronto Metropolitan University Thrill Design Invitational, we worked a modified core hours schedule while our classmates were away. Despite no faculty in the building and no playtesters to be found, it was still a very productive week, and we were actually able to work efficiently enough for a four-day weekend!
Puzzle Design
Nolan’s wheel-based puzzle design took off this week! Our reed switches arrived, and they are proving to fit very well with Cleo’s lighting control program. The idea is that when the wheel is turned to the correct position, the reed switch will change the lighting design to indicate one of the three eggs. Then, the player will tap the corresponding dragon scale on an RFID Phidget tap point built into the puzzle structure. For now, the puzzle is cardboard, but ultimately we hope to have a larger diameter wooden wheel, with laser cut magic symbols to indicate the wheel’s position.
Our biggest challenge is going to be the cluing for the puzzle. Kat has started drafting a riddle poem that we can test out at next Tuesday’s playtest evening. We are still not sure how to present this to the players, since it is certainly true that it’s hard to get guests to read, but also hard for them to retain clues to a puzzle if they don’t have something physical to refer to. We will playtest a few different methods of cluing in the coming weeks
Video Design
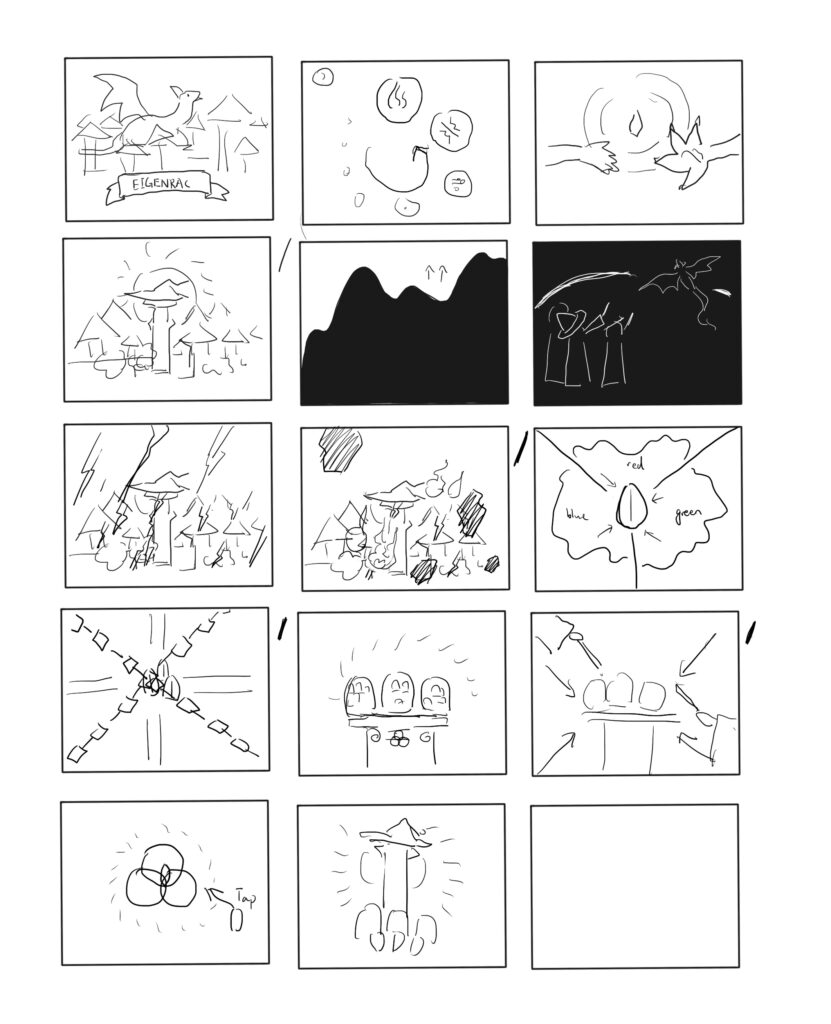
With the script for the preshow video locked down, Ivy drew a storyboard for it and began producing illustrated assets for it!
We also saw progress on the post-show video of the three baby dragons flying with their mother, and more generally, problem-solved regarding the post-show projections.
Our very first prototype of a mount for the projection surface was balancing it between two of our room’s stacking chairs at a 45 degree angle. This looked good, but we couldn’t figure out how to stabilize it, and couldn’t figure out how to hide the chairs from guests.
So, we constructed a cardboard column for the round projection surface to rest on. This didn’t look great, and presented several new problems. The projector needs to be very far back in order to project at a 45 degree angle on a circular surface, and cutting out enough cardboard from the back for the image makes the column unstable. And even beyond that, constructing an ellipse-shaped column with a 45 degree angle cutout is a very frustrating process that really takes the rapid out of prototyping. We were nearly ready to abandon the good user experience of a 45 degree angle projection, at an accessible height for kids and adults, and just go with a normal, vertical projection.
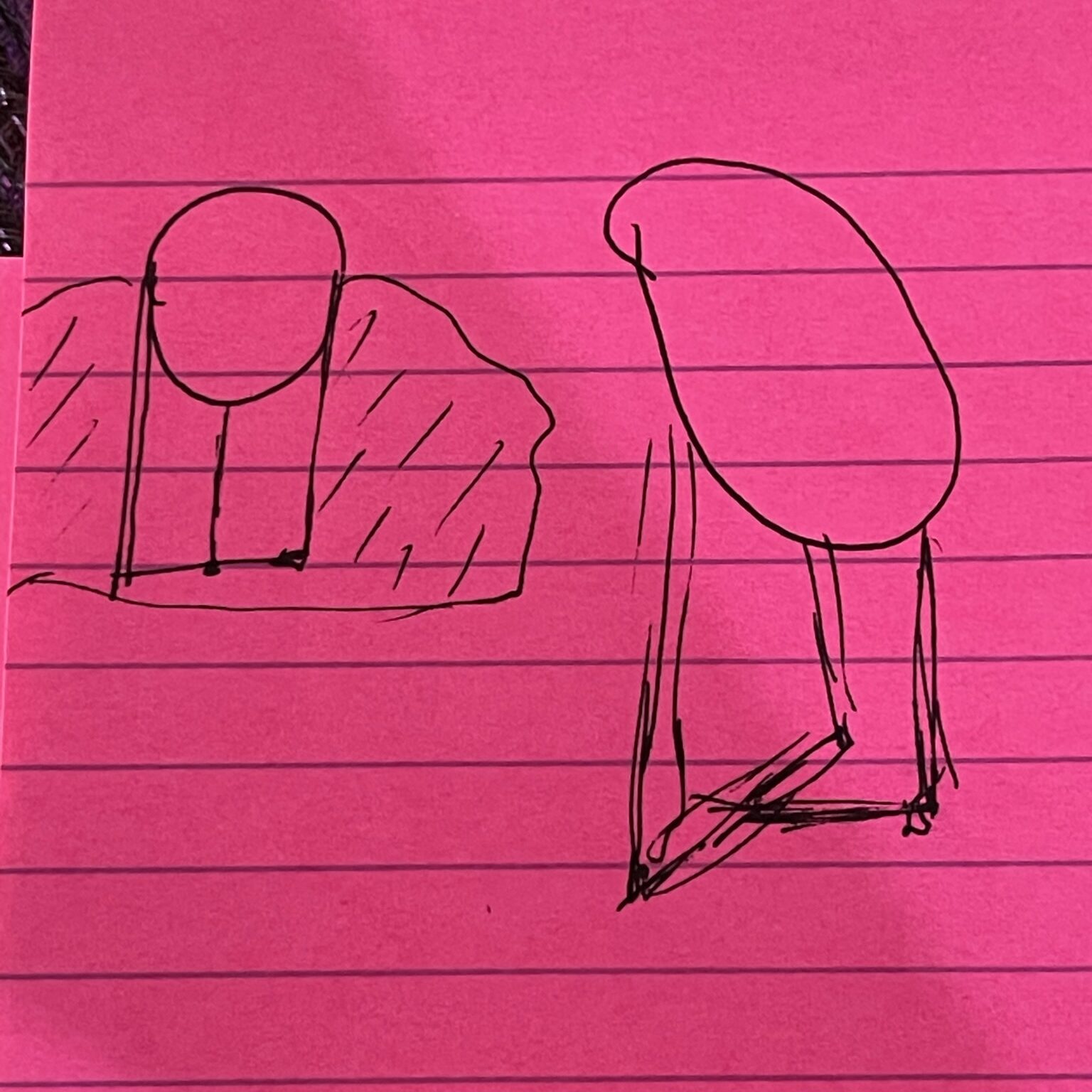
We called Christine Barnes for advice, and through that conversation we thought about what we liked about a 45 degree angle projection, what we liked about the chair based prototype, and what we actually disliked about the cardboard column. She helped us realize that we can create a wooden structure that maintains the openness of the chair-based prototype, with none of the frustrating math of the cardboard column. We will only need three measurements to construct it, and it should adhere well to our existing projection frames. Here’s a basic sketch of the idea!
Technology
Nolan constructed a hose jig for the fog machine with the help of Dave Purta, to be able to direct the fog horizontally out of the dragon’s mouth. It isn’t perfect, and gets quite hot, so we will still need to iterate for better solutions. Here is a demo video!
Cleo finished setting up the RFID phidgets as well! We discovered that Phidget RFID tags need to be written first before read, and used this protocol to write up to 24 ASCII characters.
Set Design
On Tuesday, we had a huge item checked off our to-do list: measurements from our pipe and drape rental vendor. Although we provided measurements to them via email, they understand how far apart their specific pipe bases need to be, and so require someone to come do more granular measurements than we were able to.
We attempted to laser-cut the eye blinking mechanism this week, but learned that all of the laser cutters in TechSpark on main campus were down for filter maintenance over Fall Break, which delayed the eye-blinking fabrication until next Monday.
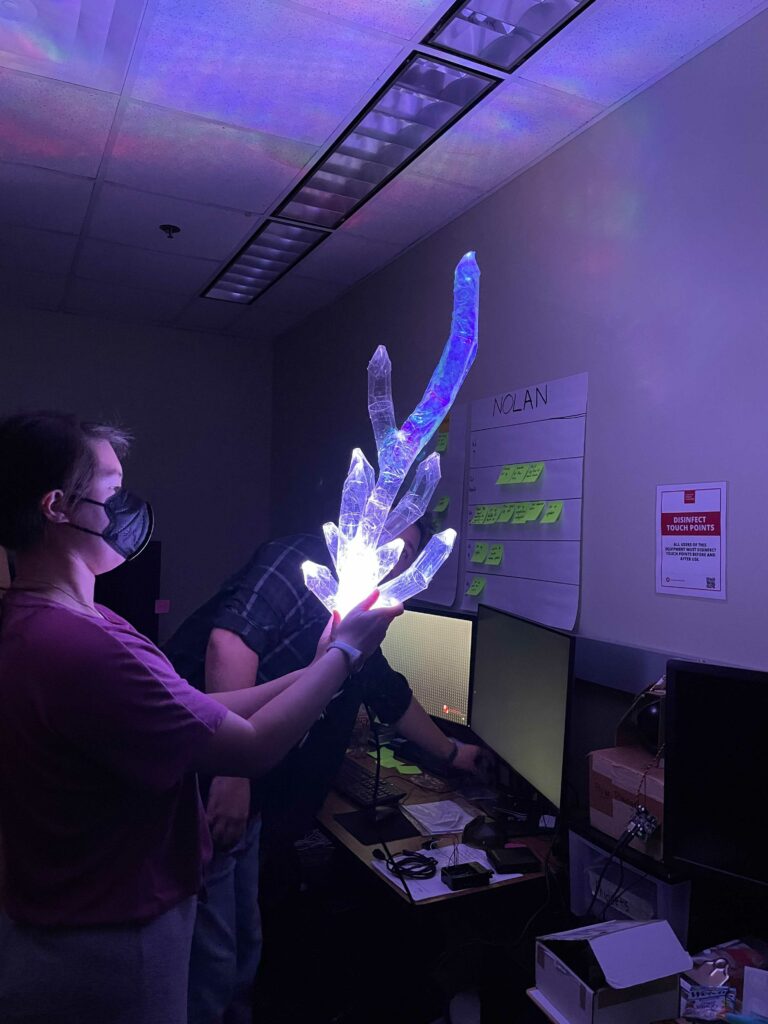
We finished covering both crystal horns with the iridescent plastic and tested them with lights that we borrowed from Dave Purta. Although we are really happy with the look, we are concerned about the amount of light bleed through the horns onto the ceiling. There doesn’t seem to be enough light diffusion through the horns. However, this is a design challenge that will move to the backburner, since it’s not critical to solve and we are feeling the time pressure of every other piece of the build.
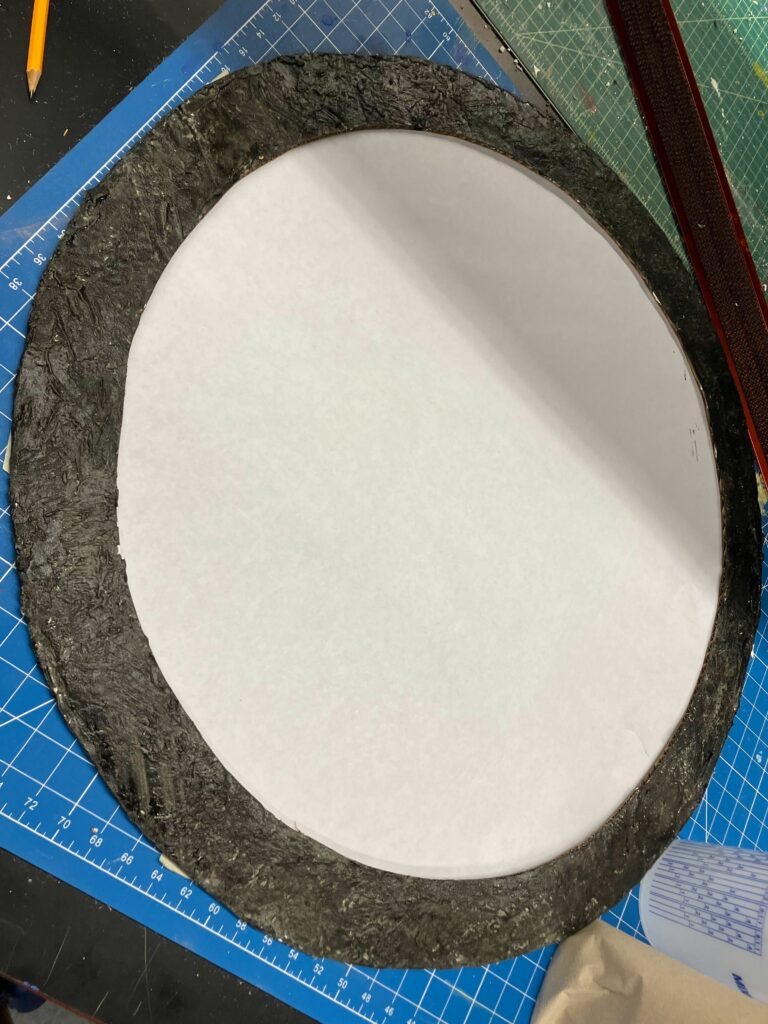
We also finished texturing three projection surface frames! We used a combination of spackle and latex paint, and later found out that that technique is called “monster mud” in the haunt industry!
Finally, we dressed the room with cardboard walls representing the structure of the room we will have at Playtest Day the Saturday after Week 8! Things are falling into place for our big milestone!
On a miscellaneous note, FMS has been keeping in contact with us regarding all ETC rooms in the center of the building getting extremely hot when heat for the building is turned on, and this week, they implemented a temporary fix for that! The paint room and tech lab are still very warm, but since our experience will have the most guests in one room at the festival, this is fantastic news.
Goals for next week:
To prepare for Playtest Day, we will need to attach our fountain, lanterns, and fans to Cleo’s show control program, iterate on our puzzle design, create playtest surveys, and finish a complete rough draft of our preshow video. This will also be the first time we have guests who are not CMU students or faculty, so running these guests through our throughput structure will be an interesting test of the project.
TL;DR
On our adjusted schedule Fall Break, we focused on constructing the wheel-based puzzle, prototyping projection screens systems, and getting the pre-show and the room layout ready for playtesting during Week 8.